世界が注目する「トヨタの動き」 生産の現場が凄かった!? 全固体電池&ギガキャスト…そして次世代BEVはどんな感じなのか
トヨタは2023年9月に現在開発中の様々な技術を具現化するためのモノづくりについて、同社の貞宝工場、明知工場、元町工場における取り組みを新たにお披露目しました。
そこまで見せて良いの? 次世代BEV&ギガキャスト&全固体電池の最前線が凄かった!
2023年6月にトヨタは「トヨタ テクニカルワークショップ」で現在開発中の様々な技術を公開しました。
そして同年9月にその技術等を具現化するためのモノづくりについて、同社の貞宝工場、明知工場、元町工場における取り組みが新たにお披露目されました。
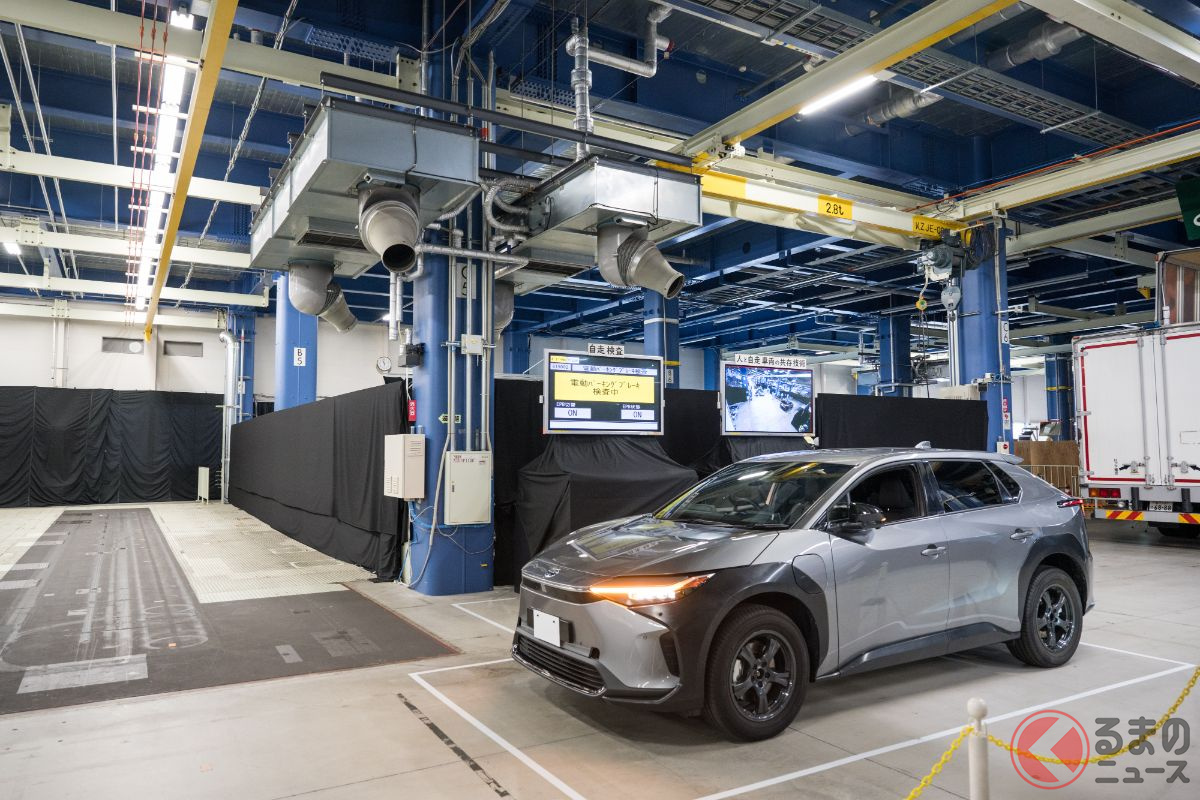
クルマづくりと言えば「新型車の開発」が注目されがちです。
しかし、クルマを開発して量産化するには設備開発・生産ライン確立・円滑な物流なども大きな要素を占めています。
そうした中で貞宝工場においては、設備づくりへの「デジタルツイン活用」が行われています。
ユーザーが欲しい商品を欲しいタイミングでデリバリーするためには、その商品を生産する生産設備をタイムリーに立ち上げることが必要です。
しかし、クルマを生産する設備づくりは、社内外の多くの人々が関わります。
さらに新たな生産設備を立ち上げる過程では、図面上では予期しなかった不具合や作業しづらい部分が見つかり、やり直しのムダが発生し、リードタイムが長くなることが課題となっていました。
その課題に対しデジタルを活用することで「設計から生産開始までのリードタイムは半分になった」と言います。
最初に3Dモデルをつくることで、設備の設計担当、製造担当、そして実際に設備を使う作業者が、事前に不具合を洗い出せるようになったようです。
これにより、トヨタの現場の知恵が設計段階から3Dモデルに織り込まれ、完成度の高い設備をやり直しなく現場に導入することが可能になりました。
また、トヨタでは新たな設備ではない既に存在する設備を3Dモデル化し、そこに現場の技を活かした改善を加えることで、短いリードタイムでの生産性向上に取り組んでいると言います。
これにより、デジタル上の改善をリアルの現場に反映させるという双方向型のデジタルツインにより、一部では作業の自動化にも繋がっています。
実際に貞宝工場の金型・設備部品加工設備では、これまで人に頼っていた材料投入などの作業を3Dモデル上で改善・自動化したことで、生産性3倍、従来比での改善リードタイム3分の1を実現しました。
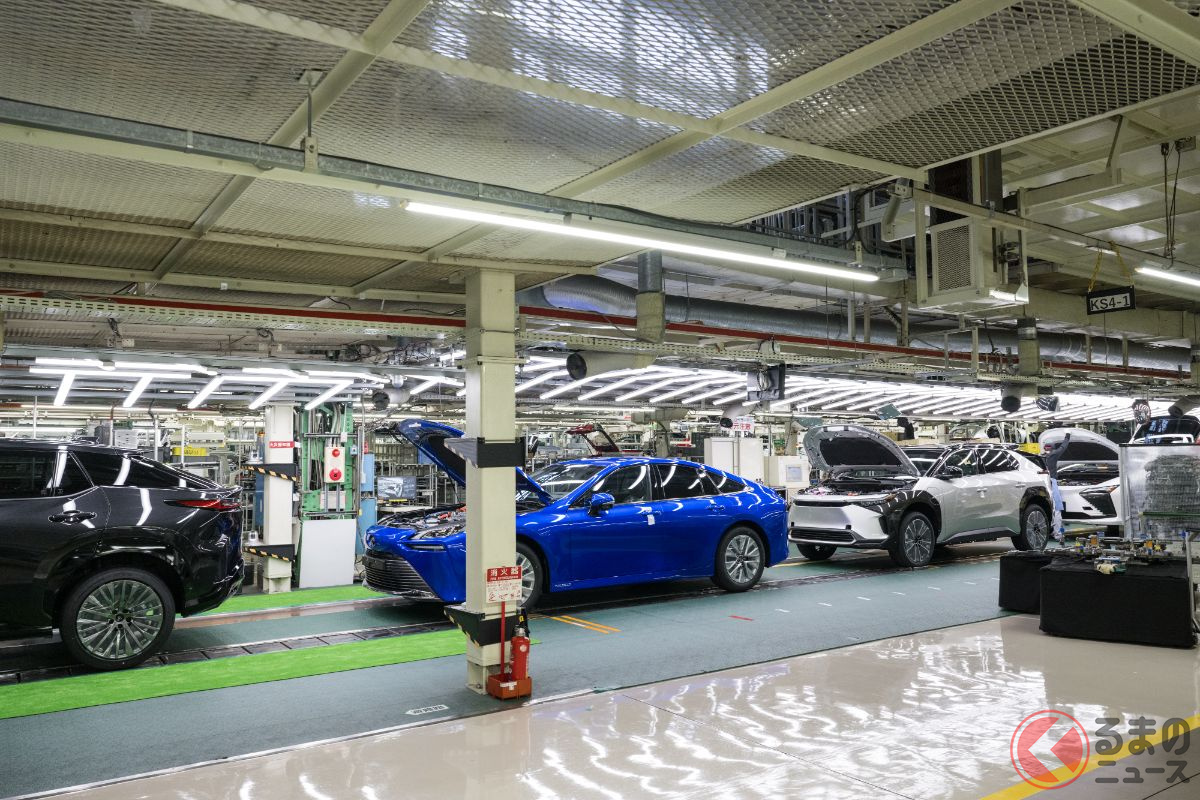
またトヨタはグローバルで年間約1000万台のクルマの量産を行っています。その支えのひとつが様々なボディタイプやパワートレーンを一緒に生産する混流生産です。
元町工場では、マルチパスウェイを支える様々な異なるボディタイプ(セダン、ミニバン、SUV)、パワートレーン(BEV、FCEV、HEV、ICE)のクルマを需要に応じて同一のラインで生産しています。
混流生産を実現のために、例えばサイズが異なる多様な車種への組付け作業を行う場合には作業位置の高さを柔軟に変えられる移動式踏み台を使用することで作業員の負荷低減に加え、作業品質の向上に貢献。
また、組立ラインでは、床面の色を黄色と緑に塗り分けることで、ラインが明るくなり、安全性や作業効率が大きく向上するなどの成果を挙げています。
なお元町工場では現在9車種が混流生産されており、ラインの作業員はそれらの異なる組み立て方法を覚えていると言い、「人」の技で支えられています。
コメント
本コメント欄は、記事に対して個々人の意見や考えを述べたり、ユーザー同士での健全な意見交換を目的としております。マナーや法令・プライバシーに配慮をしコメントするようにお願いいたします。 なお、不適切な内容や表現であると判断した投稿は削除する場合がございます。