【初公開】スズキスペーシアギアがレトロ基調に!DAMDのデザインは何が違う?時流に乗ったこだわりデザインと最新のエアロパーツ制作工程とは【PR】
ひとつでも愛車につけるだけで、印象がガラッと変わるエアロパーツ。今回はそんなエアロパーツの制作工程に迫ります。教えてくれるのは、エアロパーツメーカーとして多くのファンを持つDAMD。最後にはいまだ未発売のパーツを公開します。
エアロパーツってどうやって作るの?デザイナーに聞いてみた
なにかひとつでも愛車につけるだけで、たちまち印象を変えて自分らしい1台に近づけてくれるエアロパーツ。
「ノーマルのままでは物足りない」、「人とちがうクルマに仕上げたい」、「好きなテイストに寄せたい」といった、ひとりひとりの理想のクルマを実現するために、最近はファッションアイテムのような感覚で、手軽に装着できるパーツが豊富に揃ってきました。
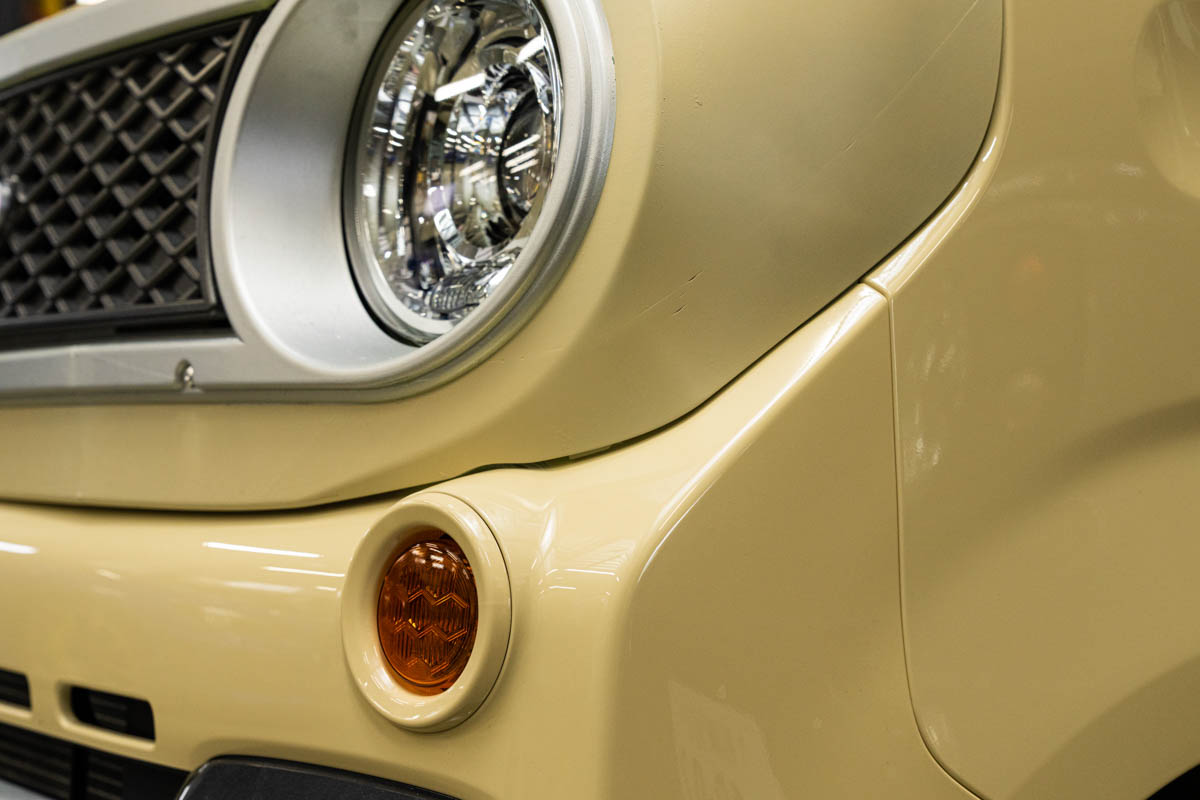
そんなエアロパーツは、いったいどのように造られているのか、気になっている人も多いと思います。
見た目を変えるだけではなく、安全性や耐久性なども考慮しなければならないはずですが、完成までにはどのような工程を経ているのでしょうか?
そんな疑問をデザイナーさんにぶつけてみたところ、その工程をすべて見せていただけることになりました。しかも最後には、2022年3月に発売予定となっている試作品をひと足早く、チラ見せしてもらえるとのこと。これは楽しみです。
登場するのはエアロパーツ・ボディキットメーカーのDAMDさん!

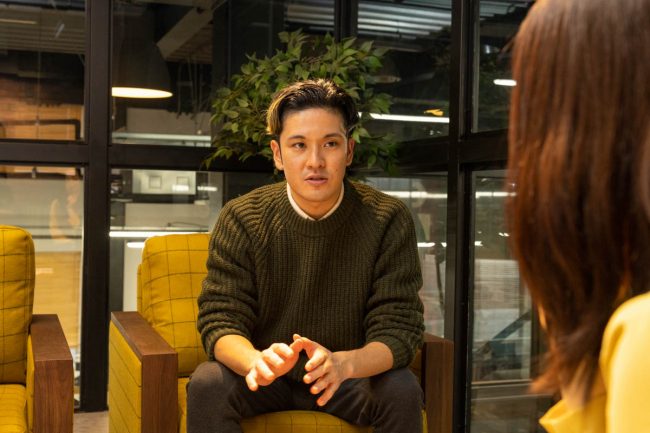
今回お邪魔したのは、エアロパーツやドレスアップパーツのメーカーとして多くのファンを持つDAMD。
1982年の創業時から、クルマが夢のあるプロダクトであり続けるために、誰もがクルマに「乗りたい!」と思えるようなカスタマイズパーツをデザイン・製作してきたメーカーです。現在も変わらず、掲げるのは「憧れを創ること。違いを創ること」。
その質感とディテールにこだわったデザインや高い品質が認められ、世界中からオーダーを受けるブランドとなっています。
そして、エアロパーツができるまでの工程をレクチャーして下さるのが、DAMDの企画開発部/デザイナーの徳田亮介さん。インタビューには代表取締役の面髙翔五さんも登場します。
デザイン工程その1「スケッチワーク」
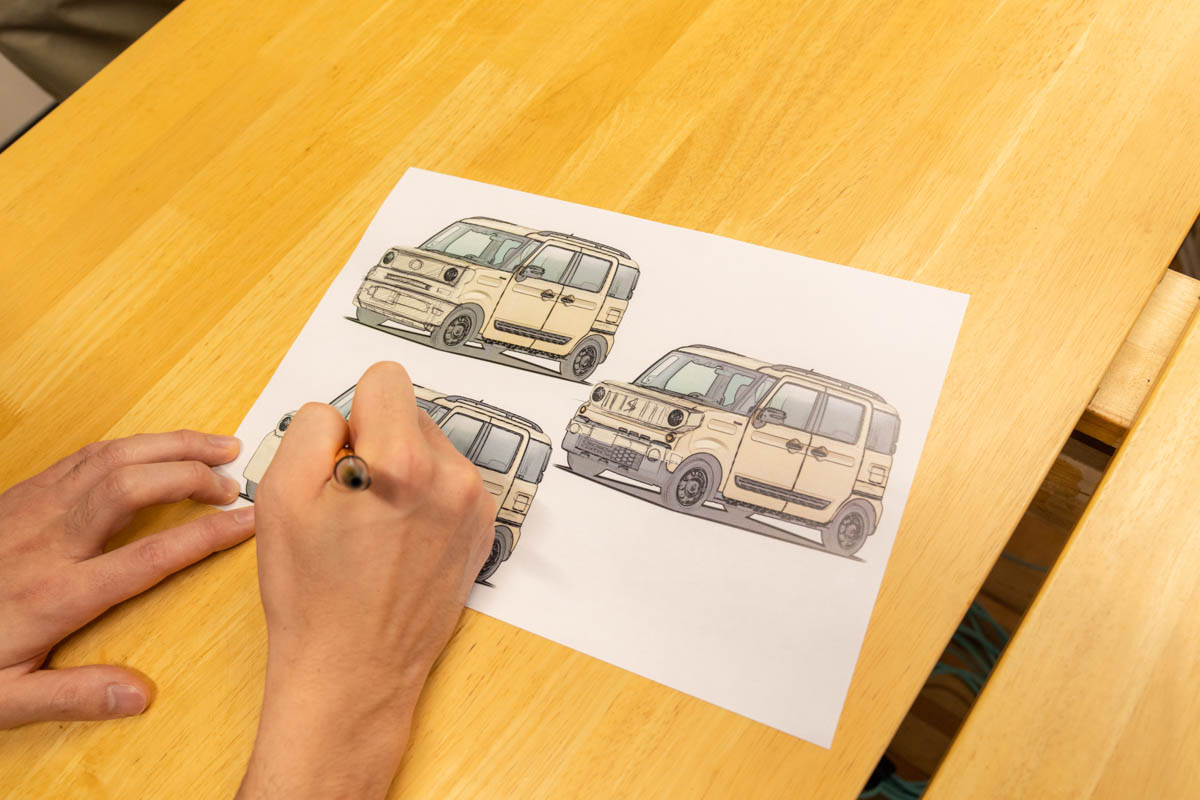
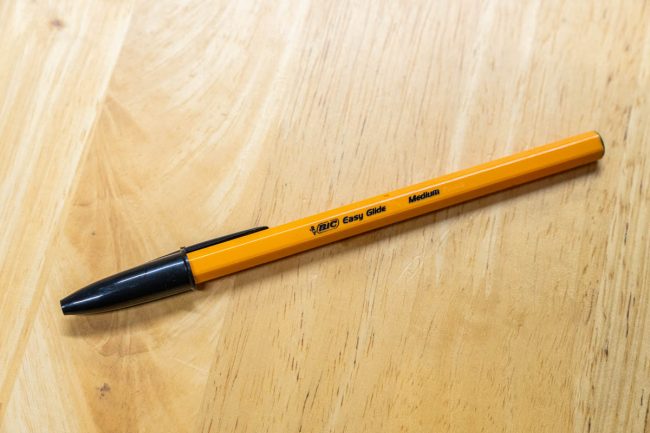
ではさっそく、デザイン工程その1「スケッチワーク」から見せてもらいましょう。
DAMDのエアロパーツは既存のクルマにあとから装着するアイテムが多いため、今回は一例としてスバル・BRZのフロントマスク部分のスケッチワークを行いました。
徳田さんが手にしたのは、1本のシンプルなボールペン。思わず「鉛筆で描くんじゃないんですか?」と聞いてしまいましたが、「そうなんです。実はスケッチワークは、“消せないこと”が重要なんです」とのこと。
鉛筆で描くとどうしても「何度でも消してやり直せる」という心構えになるため、線に勢いがなくいいスケッチができないというのです。1本1本の線に魂を込めて、長い線を本気で描いていくことが大切なのだそう。
自分自身のテンションを上げて描くことも効果的で、徳田さんはいつもヘッドフォンで音楽をガンガンにかけながら、多い時には1日でボールペン2本を使い切ってしまうくらい、たくさん描くという話にビックリでした。
何もない状態から、どうやってスケッチのアイディアを出すのかが気になるところですが、最初は好きなクルマやデザインへのオマージュから線を引いていったり、そのクルマのコンセプトを考えて個性を強める方向性にいくか、逆にまったく別の方向性にいったりすることもあるとのこと。
もともとのボディラインとどれだけ上手くつながるか、整合性が取れるかにこだわるのも欠かせないポイントだと言います。
徳田さんの手元を見ていると、サササっとものの5分くらいで新たなフロントグリルが浮かび上がり、この世になかったクルマが誕生していく様子にただただ感心するばかり。
試しに私もトライしてみましたが、「こうしたい」という理想はあってもそれを紙に表現し、さらにもとのボディとのつながりまで考えて描くというのは至難の業。
しかも、製品化を目指して描くスケッチなので、本来は製品になる際に組み込まれる付属品や、奥行きがどのくらいか、といった細かな要件まで考えながら描くことになります。ただデザインすればいいのではなく、クルマの構造などもよく理解していないとできない作業だと実感しました。
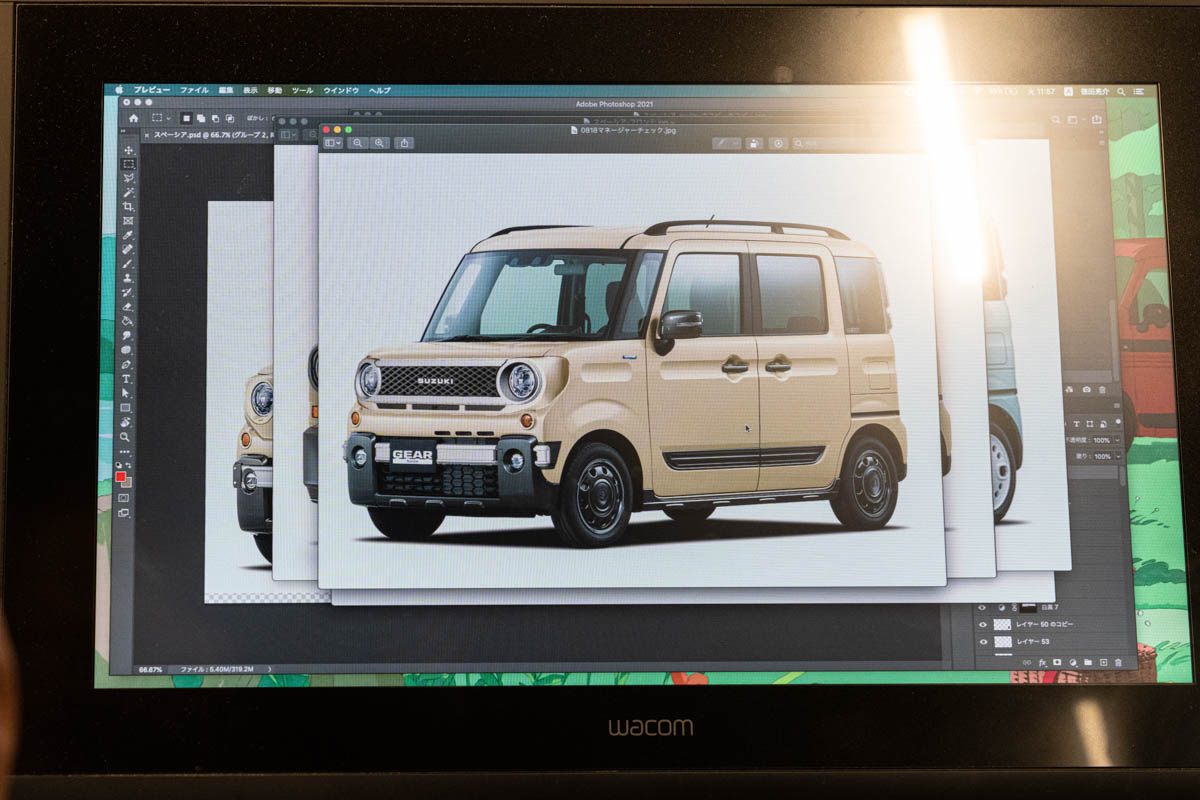
そしてだいたいのデザインが決まったら、液晶タブレットで色付けし、完成予想図を仕上げていきます。この時にはすでに、ライトやステーなど実際に製品化される際の設定も頭に入れて描くとのこと。
面の動きなどを陰影で表現し、モデラーさんが作る際にわかりやすく仕上げるのも大切なポイントだということです。フォトショップを使いこなして簡素化された作業とはいえ、1枚を仕上げるのに4~5時間はかかるという、とても大変な工程でした。
デザイン工程その2「3Dモデリング&指示連携」
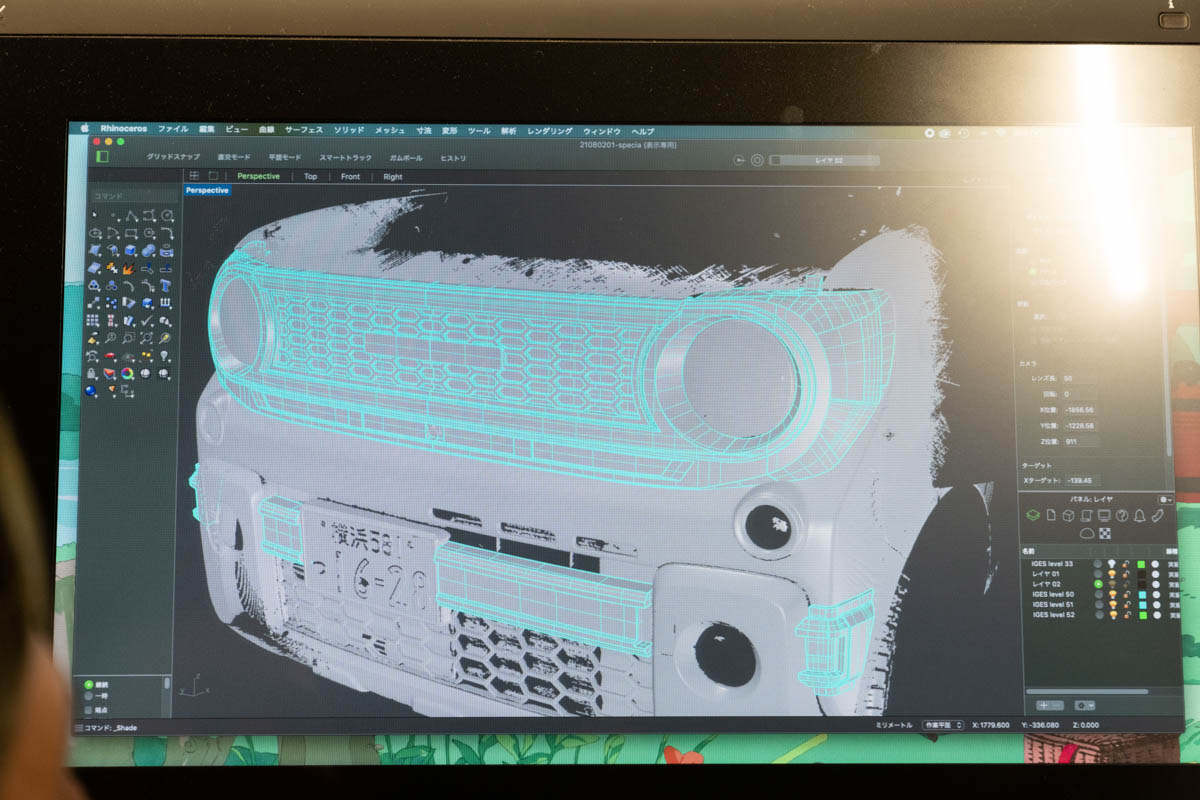
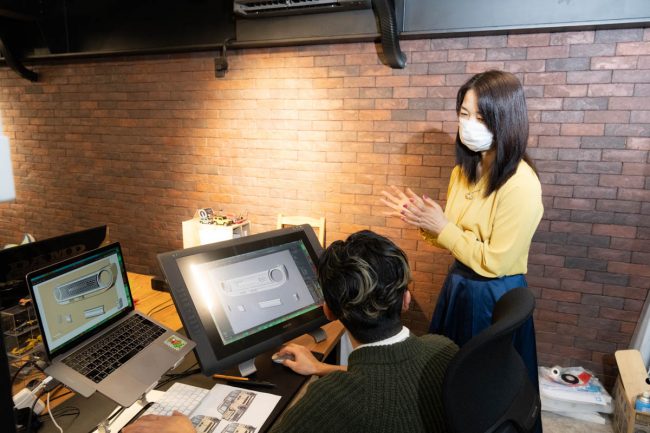
続いてデザイン工程その2「3Dモデリング&指示連携」に移ります。長い時間をかけてコツコツと仕上げた完成予想図を、今度は実際の製品を想定した3Dデータに起こしていく工程です。
実車から取り外したパーツをスキャニングし、細部までのサイズを計測。そのサイズに合わせて立体化していきますが、「ここで難しいのは数値上では間違っていないのに、目で見ると膨らみすぎてしまったり、凹んで見えてしまうといった、目の錯覚による違和感が出てしまうところなんです」と徳田さん。
折れて見えたり、一部分だけ色が濃く見えるなど、やはり平面図ではわからなかった様々な問題が浮き彫りになると言います。それらをひとつひとつ、ミリ単位で位置を指示して修正していくのがこの工程のキモとなるところ。
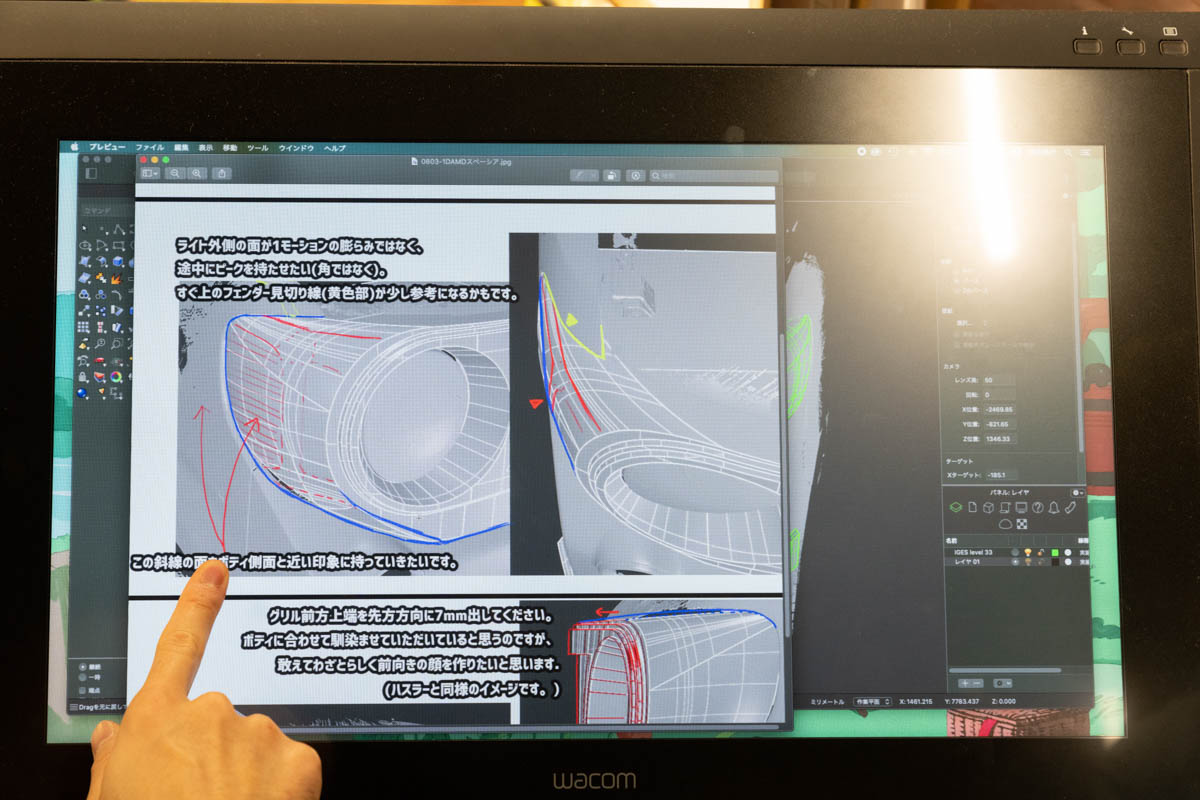
この後、実物にした際に出そうな、予測できる問題も想定して対策を施しておくこともあるそう。デザイナーとモデラー双方の経験と知見が活かされる工程でもあると感じました。
そうしたやりとりがだいたい1か月くらい続き、ようやく完成に近づいてきたところで、今度はパーツを取り付ける際の両面テープの位置なども想定して、仕上げていくとのこと。
最後に全体のイメージを含めた絵を描き、この時点でプレスリリースの準備もスタートするそうです。
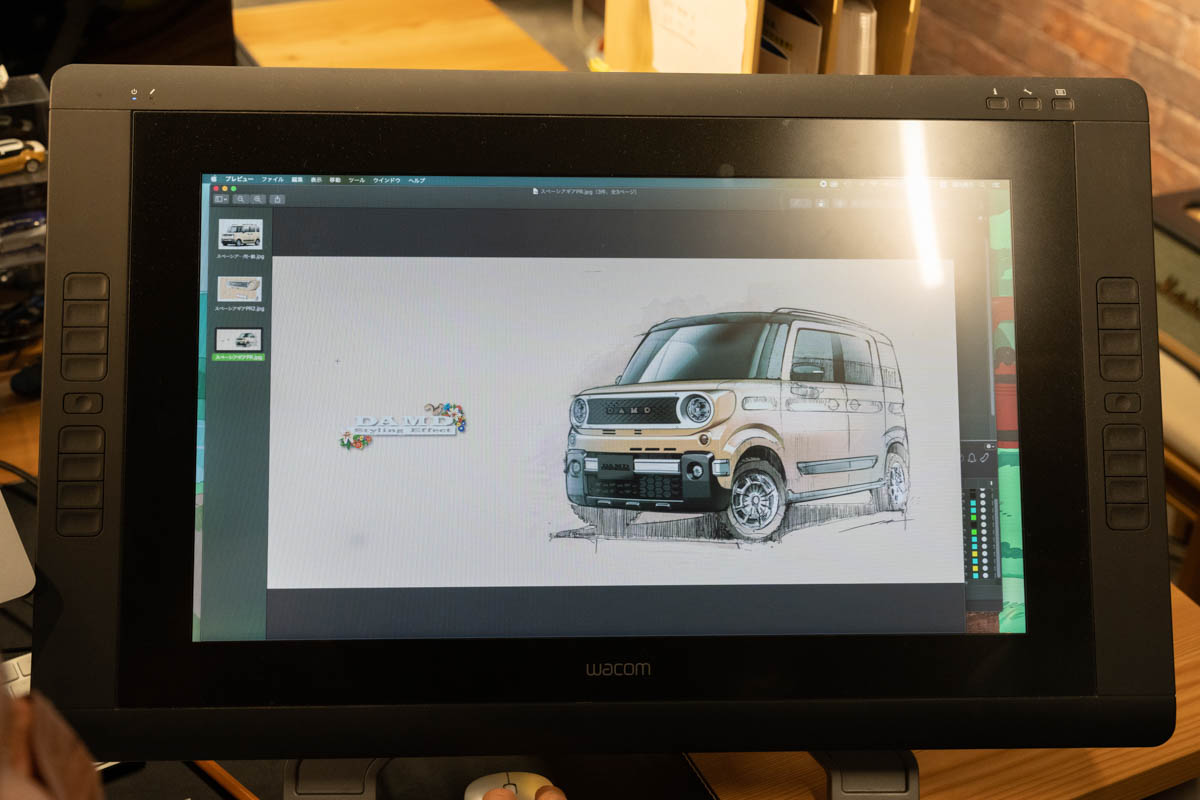
デザイン工程その3「1/1スケール3Dプリント-造形&設計検証」
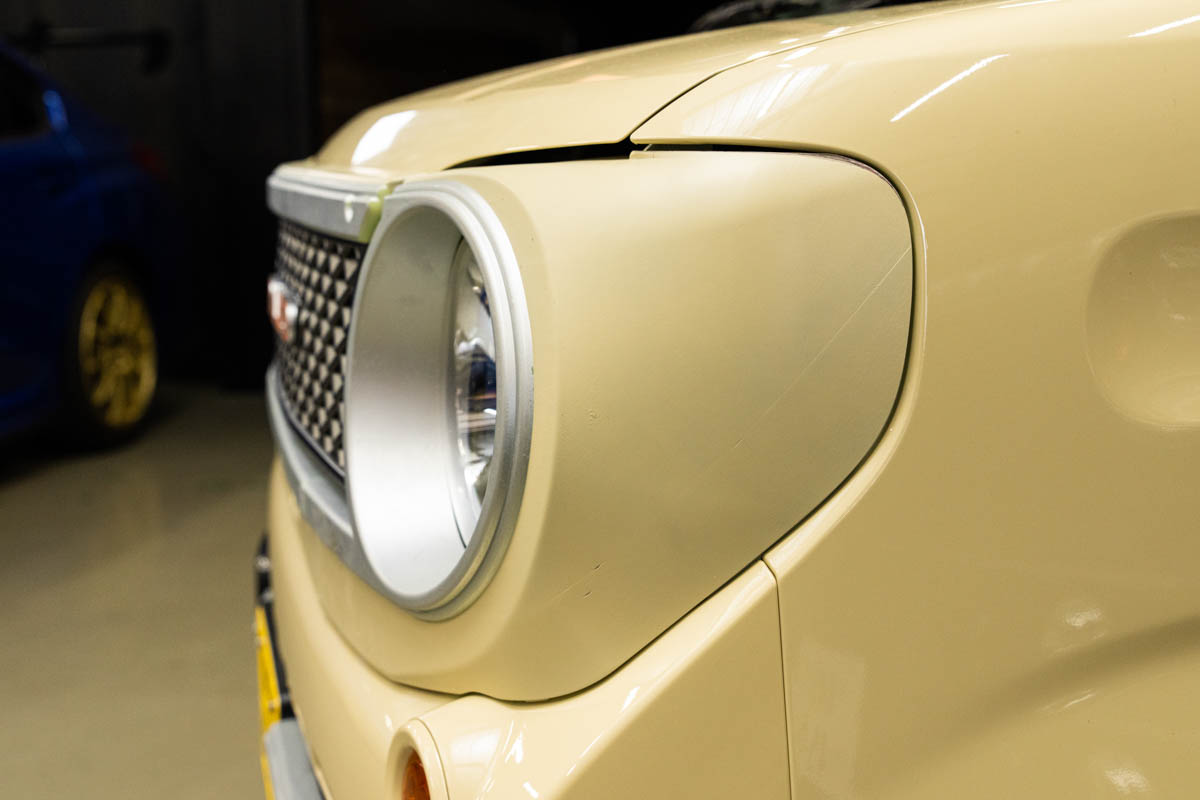
そしてデザイン工程その3「1/1スケール3Dプリント・造形&設計検証」に入ります。
まず、完成した3Dデータで実際の製品と同じ1/1スケールの3Dプリントを出力します。
実際のカラーと同じ塗装をして、実車に装着。素人目にはすんなりOKとなりそうですが、ここで再びさまざまな問題が発覚するというから驚きです。
例えば実際に社内チェックにて指摘された点としては、ヘッドライトとグリルの隙間が大きいことや、ボンネットを閉めた時に少し見えるはみ出し、グリルの端が少しボディに当たっているところなど。
「あれだけデータ上で修正を繰り返してきても、やっぱり装着してみないとわからないことがあるんです」と徳田さん。そうした問題点をあぶり出し、修正を加えてまた装着してチェックするという、地道な作業が続きます。
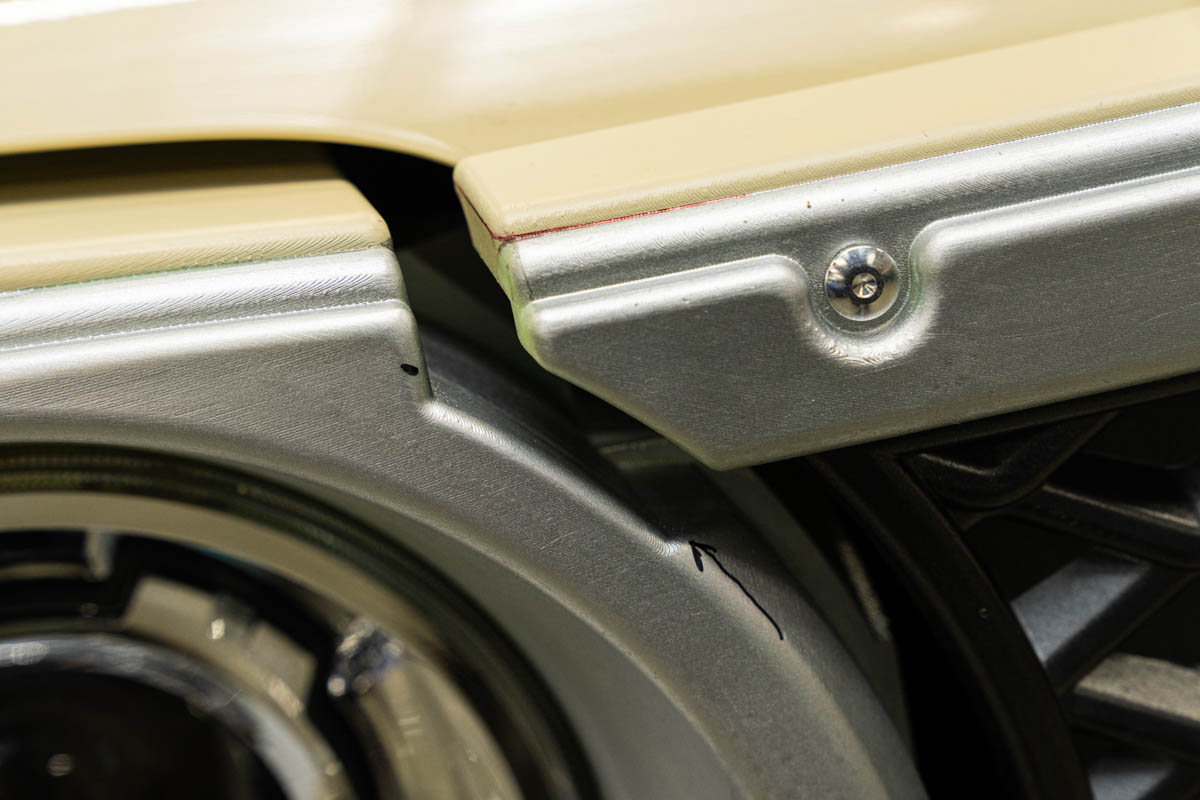
ここで細かなデータ修正を行い、OKが出ると、いよいよ市販版の金型製作に入ります。
金型完成後、T0(トライ0=最初の試作品)からT2(トライ2=2度の改良を経た試作品)を経て最終チェックに入り、同時に取り付けやすさなども入念にチェックするそうです。
過酷な環境にも耐えうる製品にするため、熱を当ててみたり、実際に走ってみて不具合が出ないかどうかまで検証を行います。
市販されるパーツは、デザイン工程その1がスタートしてから、だいたい半年くらいかけて完成するとのことで、普段は何気なく見ていたパーツひとつひとつにこれだけの苦労と情熱が注がれていることに、あらためて感服しました。
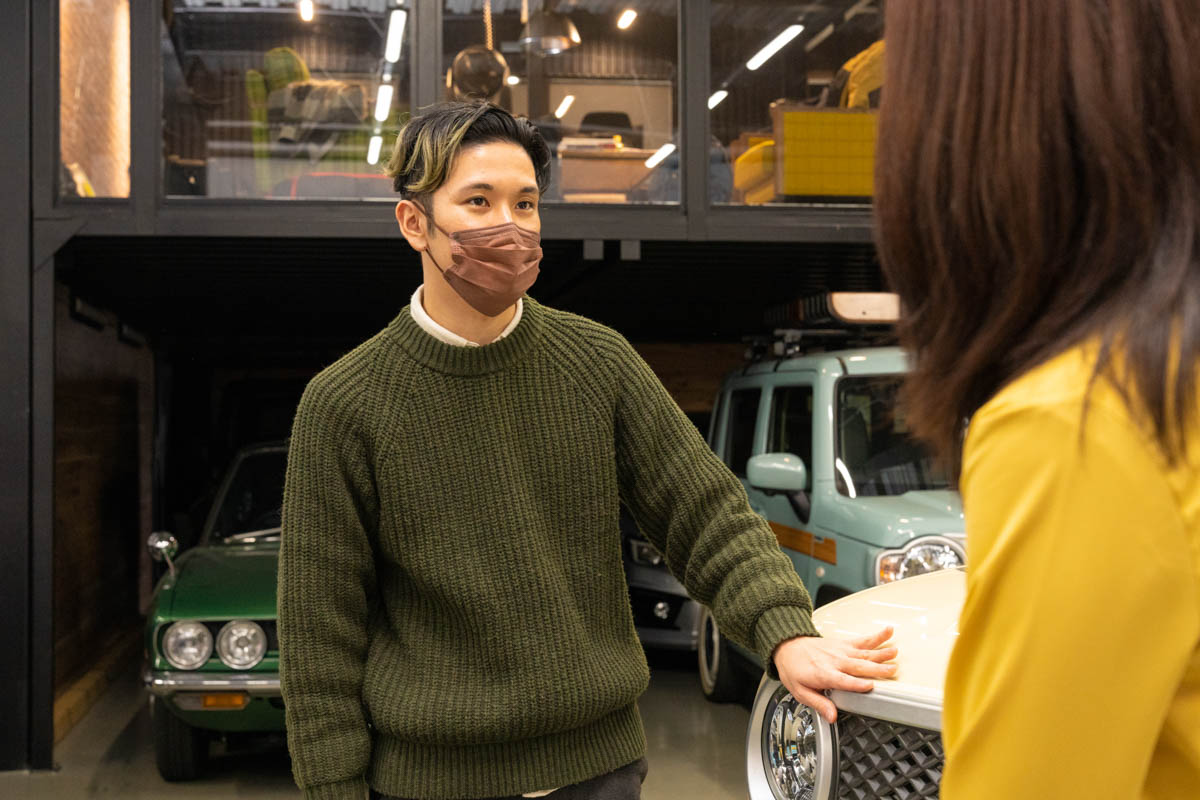
……としみじみしていると、徳田さんがひと言。
「実は、僕たちの仕事は販売したら終わりではないんです。これだけやっても、ユーザーさんから気になる点のご指摘を受けることもあるので、お客様からの声をフィードバックして、マイナーチェンジしたりしています。
それほど、日常使いの環境は想像以上に過酷だということですね。取扱説明書の用語がわかりにくいとか、取り付けが難しいといったところも、改善していくのが僕たちの務めだと思っています」
出したら終わりではなく、ずっとそのパーツの行方を見守り、責任を持ってさらに良い製品に育てていくという、DAMDの素晴らしい企業理念も知ることができました。